In 1948, 11-year-old Bob Gore packed up for Boy Scout camp. A tall boy with white-blond hair, Bob was the eldest of five children in an outdoor-oriented family. He carried a rather unremarkable list of supplies to camp that year, among them a homemade backpack and sleeping bag designed by his father and sewn by his mother.
Affordable, child-sized outdoor equipment was hard to come by back then, and the Gores’ practice of crafting what they could not buy was a habit shared by many outdoor enthusiasts. But in the case of the Gore family, this penchant for experimentation would leave a remarkable legacy.
Like his father, the young scout would grow up to become a chemical engineer, one whose serendipitous laboratory experiment would revolutionize the American outdoor experience. Thanks to Gore-Tex—the waterproof, breathable material that would become nearly synonymous with wearable rain protection—Americans began to believe that purchasing high-priced attire was the first stop on the way back to nature. Gore’s invention perfectly symbolizes a modern paradox: Americans’ escape to the woods is also an exercise in high-tech consumption.
The story of Gore-Tex and how it changed time spent in the great outdoors begins with Bob Gore’s father, Bill.
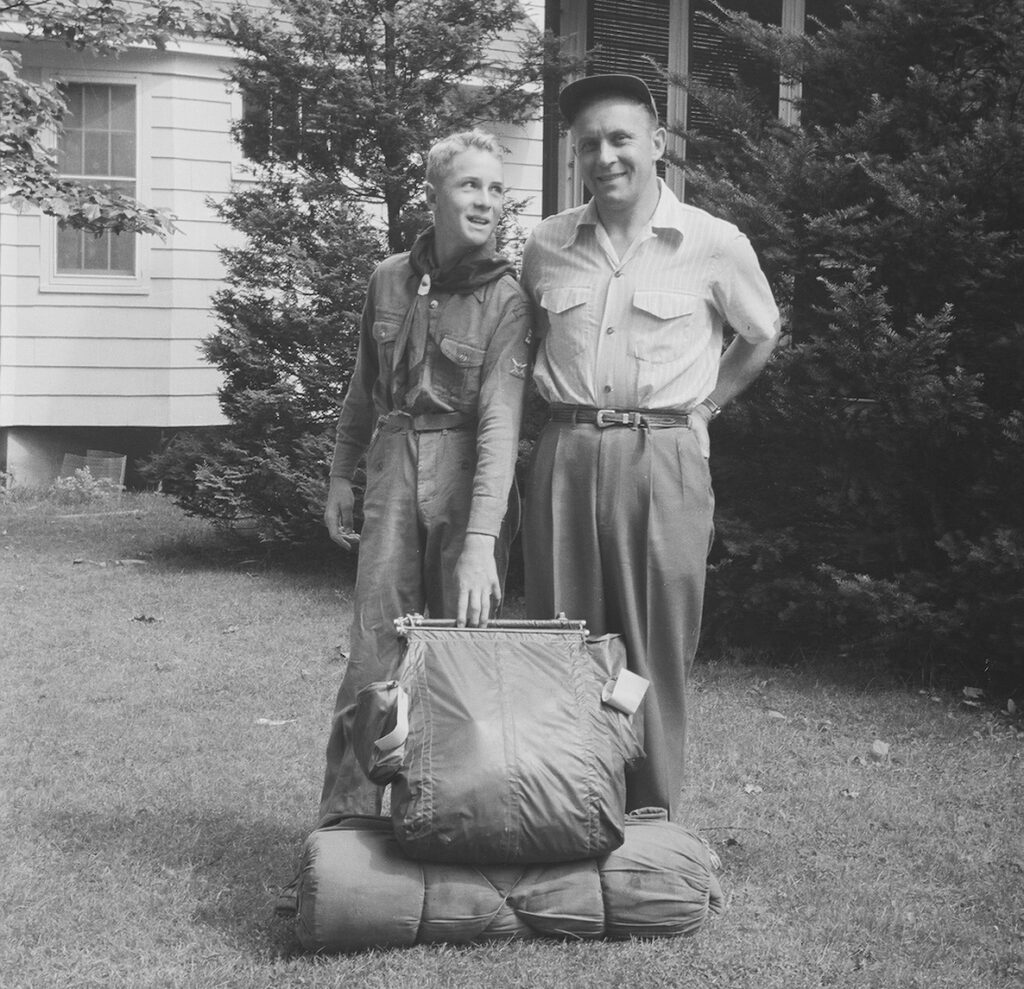
While studying at the University of Utah in the early 1930s, Bill Gore spent his spare time climbing and skiing the nearby mountains. Along with his future wife, Vieve, he got a job as a demonstrator skier at Jackson Hole, Wyoming. Demonstrator skiers climbed up mountains and skied down “just to show it could be done,” he later remembered. There wasn’t much of a future in skiing, Bill realized, so his study of physical chemistry and chemical engineering determined his next steps.
In 1945, after a stint as a chemical engineer at the American Smelting and Refining Company, Bill moved east to take a job at the chemical giant DuPont, which was just beginning to transition from military production to making synthetic materials for the domestic market. First nylon, and then a long list of other new DuPont inventions offered consumers “better living through chemistry.”
Bill eventually landed in DuPont’s plastics division, where he experimented with the polymer polytetrafluoroethylene (PTFE). Consumers know the polymer by its trade name, Teflon, the coating for DuPont’s line of nonstick cookware.
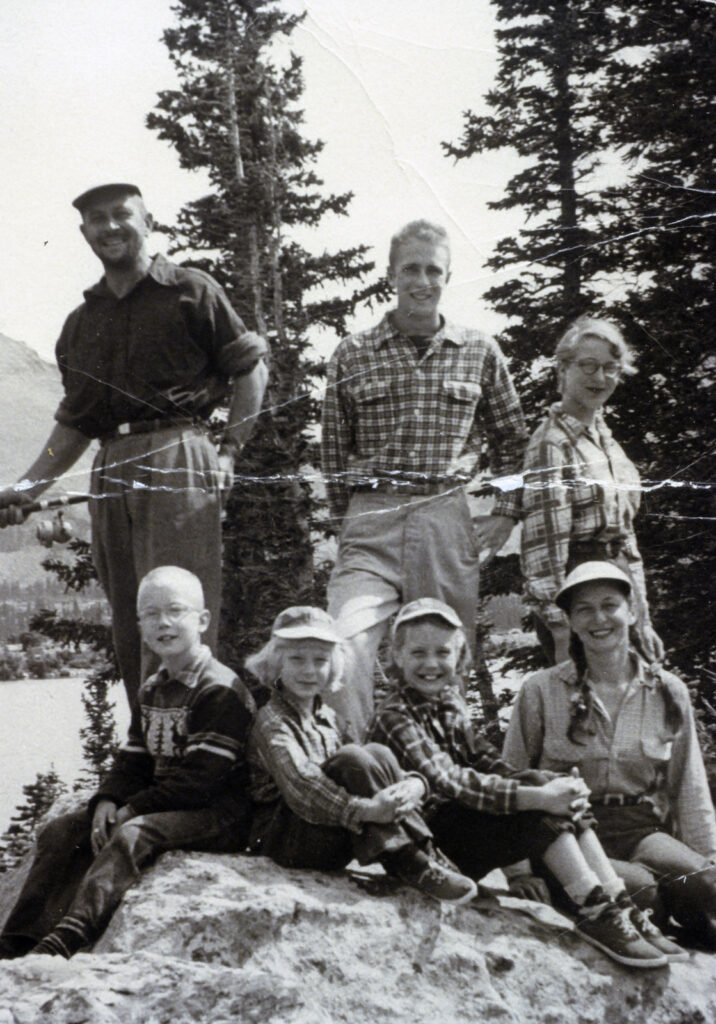
Despite the demands of his work and a growing family, Bill maintained his love for the outdoors. On weekends he liked to tinker with camping equipment, experimenting with materials from his workweek. Gore’s background helped him access special supplies not readily available to other basement experimenters. In 1945, for example, Gore ordered coated nylon from the Cordo Chemical Company so he could try out an idea for inflatable sleeping mats. Over the next decade, Bill enlisted Vieve and their children as test subjects for these inventions during family vacations.
Most memorable were the designs that didn’t work quite as intended. One camping trip in particular, to the mountains in Utah in 1948, is enshrined in family lore. Before the trip Bill had created a tent made of transparent plastic so that he and Bob could see the stars at night as they fell asleep. But the tent created a bonding experience of a different kind. The tent walls had a technical problem: they were impermeable to water vapor. Bob later remembered that it
Eventually Bill became convinced that, though DuPont found great success in making Teflon for cookware, the company was unwilling to pursue the full potential of PTFE. Seeing an opportunity himself, he left DuPont in 1957 to start the chemical company that bears his name.
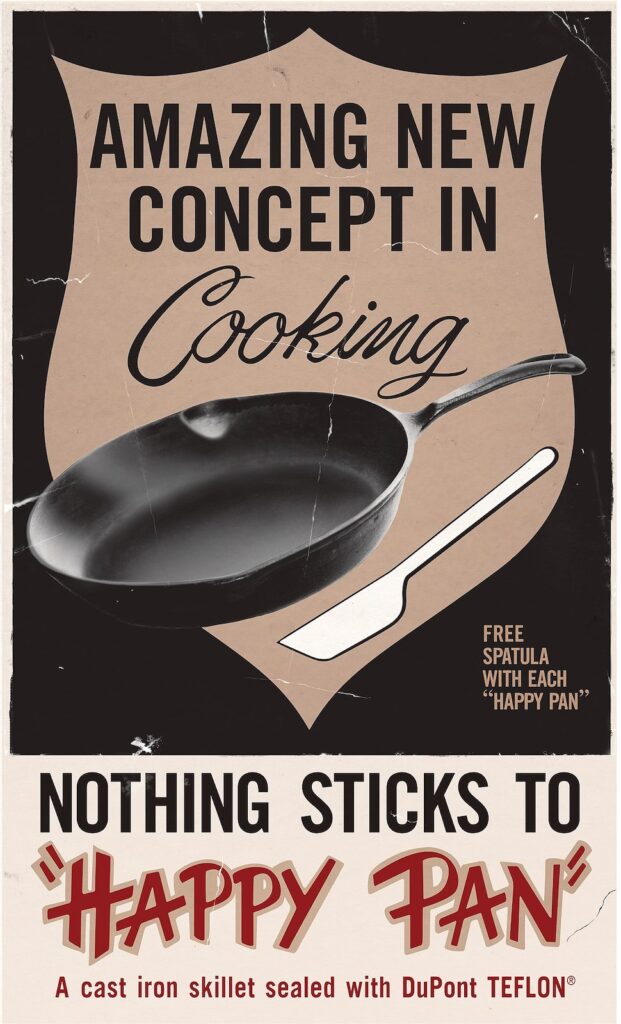
When Bob joined his father’s company, W. L. Gore and Associates, in 1963, the business had already used PTFE successfully in a range of industrial applications. PTFE was nonreactive and it repelled water. These properties made it useful as a thread sealant, for wiring, and for other objects and places likely to corrode or fatigue. But while it was well-suited to extreme conditions—NASA used PTFE fibers on the outermost layer of the Apollo space suit—the material still hadn’t found much of a place in everyday domestic life. Bob’s task was to find new applications suited for both the industrial and consumer markets.
It would be simplistic to draw a direct line from the impermeable plastic tent in the Utah mountains that failed to keep Bill and Bob dry to the invention of Gore-Tex. An old DuPont marketing study suggested a long list of applications for a sheet of PTFE, so the Gores were not the only ones to see the connection between PTFE’s properties and potential customers. Nonetheless, memories of his father’s failed experiments remained prominent in Bob’s mind as he imagined what a miracle material might do, and their experiences outdoors set part of the agenda of what he was looking for in the lab.
In 1969 Bob set his mind to making PTFE more usable in a sheet form, which could then be turned into an improved and cheaper-to-produce pipe-thread tape. The best way to do that was by stretching it. With thick oven mitts to protect his hands, he would slowly and carefully pull thin white rods of PTFE night after night, trying to expand the polymer. But the cords kept breaking. One evening he got so fed up that he just yanked a cord out of frustration. When he pulled quickly, he was surprised to find the PTFE cord stretched as wide as his outstretched arms. The next morning Bob called his father in to see how the extruded material expanded when stretched; they both recognized it as the future of the company. Bob had discovered the material that would become Gore-Tex almost by accident.
Plastics World, the trade magazine of the plastics industry, announced the next year that expanded polytetrafluoroethylene (ePTFE) was “a whole new ball game.” It could be made into yarn and fabric, films and sheeting, core insulators for cables, and tubes of all sizes. The new structure of ePTFE—it was 70% air—allowed great control over the porosity of the material. Under a microscope, ePTFE looked like a maze of webbing. The semi-permeability of the pores, along with the material’s water-repelling qualities, finally made a rain jacket or tent that ventilated and shed water seem possible.