Producers Case Study
The Changing Geography of Rare Earth Element Production
Introduction
The locations where rare earth elements are produced changed repeatedly throughout the 1900s and early 2000s. This variation suggests that production is not determined primarily by the geographic location of rare earth ores. Instead, the location of mines and separation plants is driven by a combination of market prices, government policies, and the actions of producers and manufacturers. As a result where and how rare earth elements are produced could change in the future.
Initial Rare Earth Metal Production
Although a mineral containing rare earth elements was identified in Sweden in 1788, it took more than 100 years for the first significant industrial product to be made using the rare earths. In the 1890s chemist Carl Auer von Welsbach developed a mantle made of a mixture of 99% thorium and 1% cerium for use with gas streetlights. More than five billion mantles were sold worldwide through the 1930s. Welsbach also developed mischmetal, a mixture of rare earth elements cerium, lanthanum, neodymium, and praseodymium. When alloyed with iron, mischmetal produced a metal that sparked when struck. It was widely used in pocket cigarette lighters as well as automobile ignition switches. The Welsbach Company mined rare earth deposits located in coastal sands in Brazil, India, and North Carolina.
India’s coastal sands are also rich in the radioactive element thorium, which is not a rare earth element. India banned the export of these sands in 1948 to preserve its thorium supply for a potential nuclear energy program. At that time the price of rare earth metals spiked until newly established mining locations briefly made South Africa the world’s leading exporter of rare earth ores in the 1950s.
The Mountain Pass Era
A new era in rare earths production began with the opening of the Mountain Pass Mine in California’s Mojave Desert in 1953. The mine and associated separations plant produced predominantly the light rare earths, including cerium, lanthanum, neodymium, praseodymium, and europium. Production increased dramatically in 1965, after the discovery that europium phosphors could be used to make a much brighter red in color television screens. The Mountain Pass Mine and the Molybdenum Corporation of America (often referred to as Molycorp) dominated world rare earth production and global exports from about 1960 until the 1990s. During the early 1990s California environmental regulators detected low-level radioactive wastewater leaking from the separation plant’s pipelines. Market prices for rare earth metals were low; Molycorp shut down the separation plant in 1998 and then the mine in 2002.
Growth of Rare Earth Production in China
The enormous expansion of rare earth production in China caused the price of rare earths to decrease. In 1927 rich rare earth deposits were discovered in rock that also included rich iron deposits at Bayan Obo, in what is now the Inner Mongolia autonomous region of China. These deposits led China to engage in a small amount of trade in rare earths with Germany in the 1930s and then with the Soviet Union in the 1950s. In 1970 ion-adsorption clays with an exceptionally high proportion of the heavy rare earth elements were discovered in scattered locations across seven provinces in southern China. China’s rare earth production languished amid the convulsions of the Great Leap Forward and the Cultural Revolution led by Mao Zedong during the 1960s and early 1970s. After Mao Zedong’s death in 1976, reform-minded leaders in China’s Communist Party took control. They began pushing through policies to promote manufacturing and global trade in order to secure political stability and establish domestic prosperity, leading to joining the World Trade Organization in 2001. The rare earth industry became a focal point for national development.
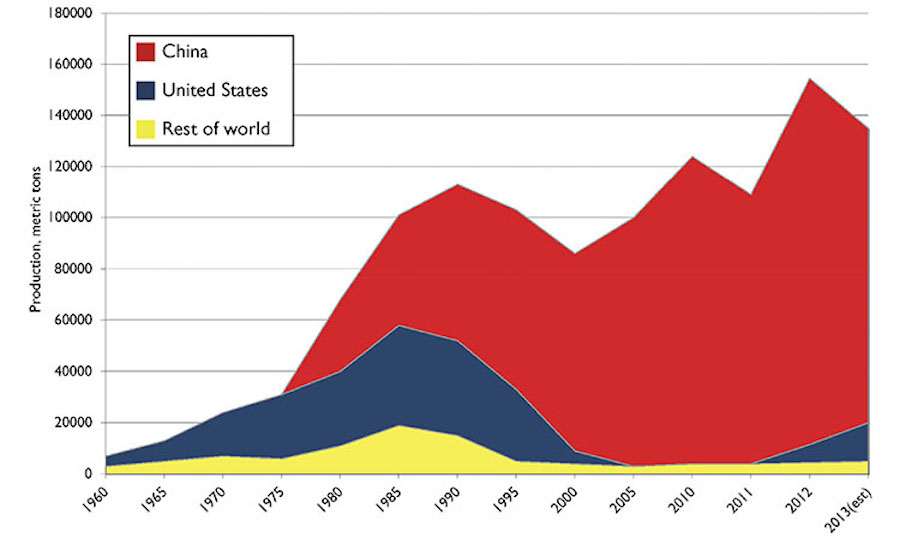
China dominates world production of rare earth oxides.
Between 1978 and 1995 China’s rare earth production increased by an average of 40% per year. Exports also increased rapidly during the 1990s, pushing prices lower worldwide. Rare earths became economical in many applications, including nickel–metal hydride batteries used in power tools and electric motors controlling automatic windows and door locks in automobiles. Corporations owned by the Chinese government sought to buy controlling stakes in foreign firms that produced rare earth metals or parts made from rare earth metals. Chinese laws restricted foreign investment in the country’s rare earth production. China became the world’s dominant producer of rare earth metals and their oxides. Rare earth oxides are the final product derived from the separation process and the form in which rare earths are delivered to manufacturers. By 2010 China accounted for 97% of production (see Chart).
China’s high level of production came at a high price, however. During the early development of the country’s rare earth industry, mining and production facilities released many pollutants, from radioactive wastewater to fluoride, which can cause bone diseases. In some villages near rare earth separation facilities in Inner Mongolia, one resident in seven has cancer. Toxic lakes near Baotou, a city near the Bayan Obo Mine, became an iconic image of the Chinese government’s willingness to sacrifice some places and groups of people for the benefit of the nation.
Rethinking Chinese Production
During the first decade of the 2000s the Chinese government began to rethink its rare earth production practices. The government sought to develop companies that could manufacture rare earth magnets and advanced electronic components in China. Beginning in 2005 the export quotas authorized by the Chinese Ministry of Trade began to decrease, limiting how much rare earth oxide could be exported to foreign manufacturers. Rare earth producers that did not comply with new environmental regulations were denied shares of the quotas. In the summer of 2010 the export quotas for the second half of the year were cut in half.
The reduced export quotas worried high-tech manufacturers outside of China. This worry turned into panic a few months later, when a scheduled shipment of rare earth oxides from China failed to arrive in Japan. Tensions between the countries were running high after a drunken Chinese fishing-boat captain had been arrested for trying to ram a Japanese coast guard ship in disputed waters. People quickly speculated that the Chinese government was manipulating rare earth exports to influence international politics. The price of the rare earth elements spiked, increasing by thousands of percentage points in a few weeks.
The high prices created by the so-called “rare earths crisis” during 2011 and 2012 prompted many companies around the world to consider producing rare earth metals. Molycorp reopened the Mountain Pass Mine and installed a $500 million separation plant designed to meet U.S. environmental standards. Lynas, which operated a separation plant in Malaysia, used a $250 million investment backed by the Japanese government to develop the Mount Weld mine in Western Australia. The Brazilian Metallurgy and Mining Company (CBMM) put into operation a process to extract rare earths from the accumulated waste of its niobium mine. Many of these operations promised to use innovative new separation processes that were less environmentally harmful (though more expensive) than the solvent extraction process that had been significantly advanced in China during the 1970s.
The bubble in rare earth prices soon burst, however, and dreams of establishing rare earth production around the world collapsed with it. In 2014 the World Trade Organization ruled that China’s export quotas were an illegitimate restraint on free trade. Abolishing the export quotas has increased the global trade of rare earths, but it has also eliminated an important tool in the Chinese government’s efforts to reduce domestic pollution. Black-market (illegal) production of rare earths remains a significant problem because unlicensed producers do not take steps to control waste or pay taxes that fund environmental monitoring and government health programs. Although international production has increased slightly since 2010, about 80% of world production still took place in China in 2018.
Conclusion
Rare earth ores of various qualities can be found in many places around the world. But which mines are developed and where the separation of rare earth metals takes place is not determined by geology alone. Instead, the changing geography of rare earth production is influenced by private companies, governments, and the increasingly global markets for these metals. This history shows that rare earth production is shaped by the decisions made by consumers, manufacturers, mining companies, and governments.
Sidebar: The Balance Problem
One issue facing producers is called the “balance problem.” Since ore contains unequal amounts of several rare earth elements, producers have trouble making enough of the more highly desirable rare earths without overproducing the most common types. For example, the light rare earth elements cerium and lanthanum make up relatively high percentages of rare earth element ores, so they sell for the lowest prices (see Table). Producers make them largely as by-products of producing higher-value rare earth metals. Terbium and europium are much less common in ore and command much higher prices.
However, the price of a metal is also driven by changing patterns in how a metal is used (demand). The price of europium dropped precipitously between 2014 and 2016 as demand for the metal decreased. In the early part of the 2010s most europium that was produced went into compact fluorescent light bulbs (CFLs). By the middle of the 2010s advances in engineering and production caused a drop in the price of LED light bulbs, which used 90% less europium than CFLs. Since it can take a decade or more for a new rare earth production facility to come fully online, these fluctuations in price are a serious challenge for rare earth element producers.
Table: Fluctuating Rare Earth Element Prices (in average dollars per kilogram)
Rare Earth Metal, with Purity Percentage | 2014 | 2015 | 2016 | 2017 | 2018 |
---|---|---|---|---|---|
Cerium oxide, 99.5% minimum |
5 |
3 |
2 |
2 |
2 |
Dysprosium oxide, 99.5% minimum |
395 |
279 |
198 |
187 |
180 |
Europium oxide, 99.99% minimum |
822 |
344 |
74 |
77 |
56 |
Lanthanum oxide, 99.5% minimum |
5 |
3 |
2 |
2 |
2 |
Mischmetal (65% cerium, 35% lanthanum) |
10 |
7 |
5 |
6 |
6 |
Neodymium oxide, 99.5% minimum |
63 |
48 |
40 |
50 |
51 |
Terbium oxide, 99.99% minimum |
713 |
564 |
415 |
501 |
461 |
(Source: U.S. Geological Survey, “Rare Earths: Mineral Commodity Summaries 2019,” p. 132.)